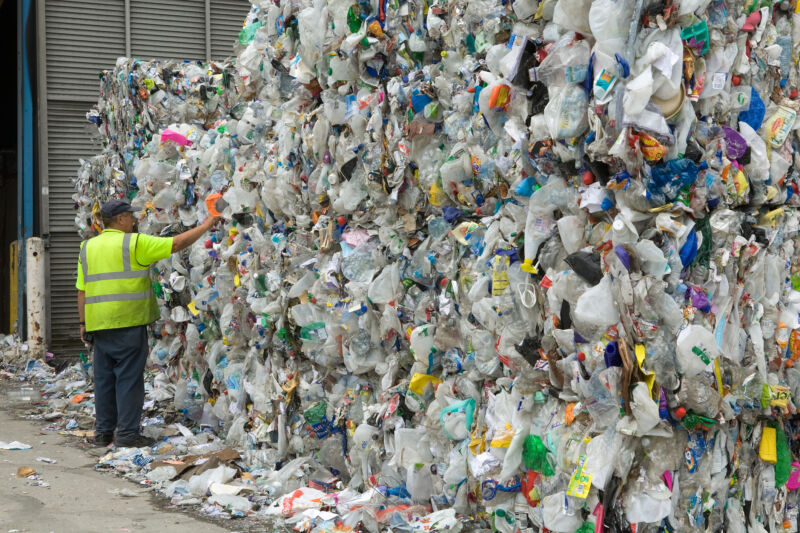
The Earth is suffocating under a tidal wave of plastic waste. The most egregious perpetrators, notorious for their lingering presence in landfills, include polypropylene, employed in food packaging, bumpers, and other applications, as well as polyethylene, prevalent in plastic bags, bottles, toys, and even mulch.
While polypropylene and polyethylene will undergo recycling, the process is expected to be arduous and occasionally yields substantial amounts of methane, a potent greenhouse gas. These polymers are polyolefins, resulting from the polymerization of ethylene and propylene, their raw materials mainly sourced from fossil fuels. The intermolecular forces binding polyolefins are notoriously difficult to break.
Researchers at the University of California, Berkeley have developed a method for recycling polymers that employs catalysts to cleave their chemical bonds, transforming them into gaseous propylene and isobutylene at room temperature. These gases can subsequently be recycled into fresh plastics.
Because polypropylene and polyethylene are notoriously difficult and expensive to distinguish from one another in a mixed waste stream, it is crucial that a recycling process be applied separately to each polyolefin, according to the research team’s recently published findings in Science.
Breaking it down
The recycling process employed by the crew is referred to as isomerizing ethanolysis, which relies on a catalyst to break down olefin polymer chains into their constituent molecules. Due to their molecular structure featuring long chains of single carbon-carbon bonds, polyethylene and polypropylene exhibit exceptional resistance to chemical reactions. Most polymers typically feature at least one carbon-carbon double bond, making them relatively easier to disrupt.
While previous attempts by these researchers to isomerize ethanol via ethenolysis had yielded limited success, the earlier catalysts – expensive metals – were prone to degrading rapidly, thereby precluding complete conversion of plastics into fuel. The novel synthesis process combining sodium-alumina with tungsten oxide on silica substrate yielded significant economies of scale and improved efficiency. However, the high processing temperatures necessary for this reaction did result in a marginal increase in overall costs.
Plastics subjected to publicity with sodium on alumina undergo a transformation in which every polymer chain is broken down into shorter polymer chains, resulting in the formation of breakable carbon-carbon double bonds at each end. Interruptions from the chains persisted relentlessly. After completing this process, each molecule was subjected to a subsequent round of olefin metathesis, commonly referred to as the second course. Researchers have discovered that exposing the material to a flow of ethylene gas, followed by reaction with tungsten oxide on silica, leads to the breaking of carbon-carbon bonds within the material.
Researchers have discovered that the process breaks all carbon-carbon bonds in polyethylene and polypropylene, releasing the carbon atoms which then link up with ethylene molecules, a crucial co-reactant according to Dr. R.J. A lead author on the study, Conk spoke with Ars Technica about their findings. The damaged hyperlinks subsequently interact with ethylene, thereby eliminating them from the molecular structure. Without the presence of ethylene, the ripening process cannot occur.
The complete cracking process involves the consecutive conversion of polyethylene into propylene, followed by the transformation of polypropylene into a mixture of propylene and isobutylene.
This technique exhibits exceptional selectivity, yielding a substantial quantity of the targeted product. Propylene, derived from polyethylene, and each propylene and isobutylene, respectively, originates from polypropylene. Propylene and isobutylene are highly sought-after chemicals, as propylene serves as a vital raw material for the chemical industry, while isobutylene is a frequently employed monomer in various polymer applications, including synthetic rubber and a fuel additive.
Mixing it up
As a result of plastic combinations often occurring at recycling facilities, the researchers sought to explore the implications of simultaneously treating polypropylene and polyethylene through isomerizing ethenolysis. The response proved lucrative, converting the mixture into a blend of propylene and isobutylene, with an almost equal proportion of propylene to isobutylene produced.
The presence of contaminants in mixtures can also take the form of additional plastics, further complicating their composition. To ensure the response remained effective, the team also investigated its performance in scenarios where contaminants were present. Scientists conducted experiments using plastic items intended for disposal, combined with a centrifuge and a bread bag holding residues from various polymers, including polypropylene and polyethylene. The reaction produced significantly fewer impurities in the form of propylene and isobutylene, compared to when using pure forms of the polyolefins.
Let’s explore the possibility of incorporating alternative plastics, such as PET and PVC, alongside polypropylene and polyethylene to observe any potential differences. The changes resulted in a substantial reduction in yield. To ensure the recycling process achieves success, all residual impurities must be meticulously removed from polypropylene and polyethylene products before they are recycled.
While this recycling method holds promise, its potential impact could be significantly amplified if scaled up on a massive level. As the analysis team expanded the experiment’s scope, the outcome surprisingly mirrored the initial findings, hinting at a positive trajectory ahead. Despite these challenges, we will need to build substantial infrastructure before we can make a dent in our plastic waste.
The researchers expressed their hopes that the studied work would yield practical approaches to generating novel polymers. “Consequently, the production requirements for essential commodity chemicals sourced from fossil fuels would likely decrease substantially, resulting in a notable reduction in related greenhouse gas emissions.”
Science, 2024. DOI: