When people think of newly poured concrete, they often envision a surface that should be allowed to dry as quickly and cleanly as possible. A cutting-edge wheeled robot navigates efficiently across terrain, simultaneously carving out a path that fortifies structures and reduces construction costs.
If large volumes of moist concrete are poured as a single, excessively deep layer, it’s likely to develop cracks due to the natural drying and contraction process. To achieve this effect, the fabric is typically layered in succession, with each layer being added once the previous one has fully hardened.
While layering may seem a promising approach, it’s essential to acknowledge the possibility that if the layers are simply stacked one upon the other, the final structure may suffer from inadequate shear strength at the interfaces between these layers? With subtle adjustments, it’s effortless to create a smooth sliding motion between adjacent layers.
As a result, concrete is carefully poured around a dense arrangement of vertically positioned steel rebar lengths. The reinforcing rods operate effectively across all layers, from top to bottom, enhancing the structure’s shear strength.
Rebar’s inclusion in a concrete mix increases its cost, as well as its overall weight. Staff typically manually create grooves on each layer’s floor while it is still damp, thereby providing additional surface area for bonding with the subsequent layer. By increasing the shear energy on the interface, a significantly lower amount of rebar is necessitated.
While the cost savings from using reduced rebar may initially appear attractive, they are largely mitigated by the increased labor hours necessitated to create the grooves, thereby rendering the overall benefit negligible. Where is the ConiRunner robotic available?
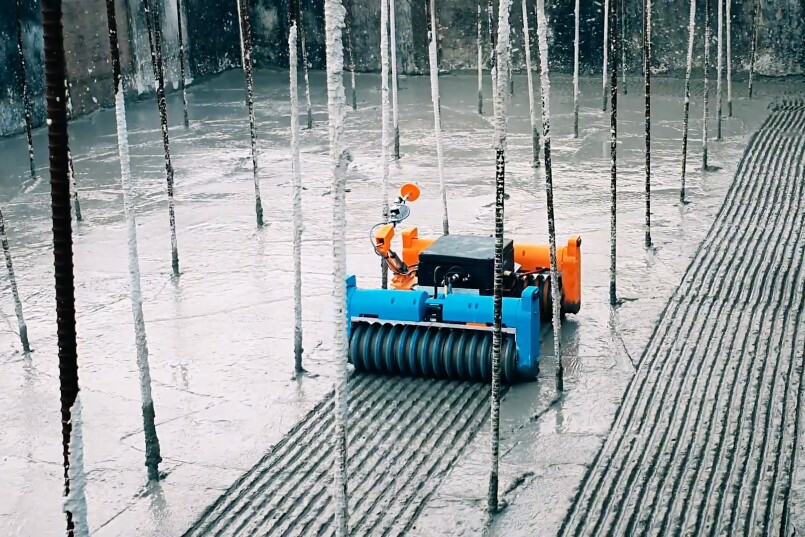
Itone
Developed through a partnership between Korean robotics firm Itone and development agency Posco E&C, the system autonomously makes its means throughout moist concrete surfaces at a pace of as much as 10 mph (16 km/h), including rows of grooves through its two 15-inch (381-mm) wheels because it does so.
With its array of sensors, including LiDAR, ultrasound, cameras, and an inertial measurement unit, the robotic navigation system expertly traverses diverse surfaces while skillfully sidestepping obstacles like rebar rows. The device is designed to gauge the concretes’ hardness, guaranteeing the material can support a load of approximately 10 kg (22 lbs), while remaining malleable enough to create grooves with a minimum depth of 0.24 inches (6 mm).
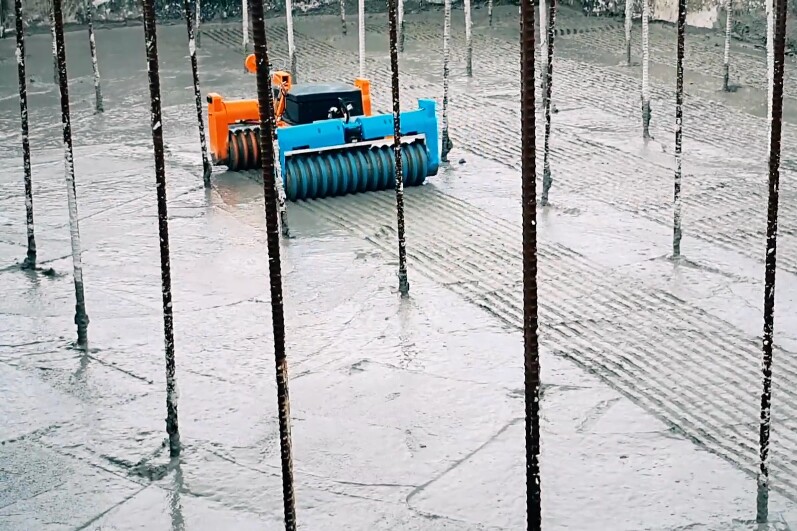
Itone
Accordingly, the Conti Runner’s deployment minimizes the need for rebar reinforcement by approximately 30% and expedites construction time by up to 85%, allegedly rivaling the efficiency of eight human workers.
When will robots see widespread adoption? You can view it in action via the accompanying video.
The CONIT Runner is a robotic solution engineered to excel in the development of websites that require precise navigation and traversal on moist concrete surfaces, showcasing its exceptional capabilities.
Supply: