Take heed to this text |

The PPE module, examined and enabled by a gantry robot, will energize the Gateway area station. Supply: Bell-Everman
NASA’s Artemis program aims to send humans back to the moon to establish a sustainable presence on its surface, with plans to construct a lunar floor base and deploy a permanent area station. The Gateway space station is expected to harness the power of its PPE module, featuring large-scale, high-efficiency multi-junction solar arrays that can generate up to 60 kilowatts of energy.
To guarantee the PPE’s triumph, it is crucial to verify the array configurations using advanced simulations that accurately replicate daytime conditions and meticulously evaluate each circuit’s performance. Designed to optimize performance, the photovoltaic simulator head units should be strategically placed at multiple points along the length and width of the solar arrays.
The typical achievement of that course is accomplished using automation frameworks comprising sequential phases. Due to the unusually large size of the PPE’s photovoltaic arrays, traditional frames designed for standard array sizes were unable to accommodate the necessary vertical and horizontal movement?
Engineered and manufactured a bespoke movement system for Angstrom Designs’ photovoltaic simulators, enabling precise testing of PPE’s solar panel performance. To ensure absolute calibration of simulator heads, we designed an I-formation gantry robot that calibrates and validates the simulator’s efficiency against photovoltaic cell specifications.
The following examination delves deeply into the mechanical obstacles involved in assembling the movement system, taking into account its unique requirements.
Bell-Everman crafts the most economical and efficient design solutions that meet clients’ needs.
An early design concept included a double bending track arrangement, with one track situated at the bottom and its counterpart approximately 30 feet away. Positioned precariously close to the very top of the panels. The custom-designed tracks enabled efficient movement of the massive 3,500-pound LED photovoltaic simulators. Loaded with versatility, this setup enables technicians to inspect a single deployed array, before traversing to the other side of a massive scaffolding structure and examining another array in situ.
Despite its potential to operate similarly to an I-formation gantry, this resolution necessitated customized bearing configurations. The heightened design intricacy ultimately propelled the project beyond its financial means, due to the stringent peak and cargo requirements.
Designing a groundbreaking movement system, Bell-Everman conceived a novel approach by utilizing a cell-based foundation for X-Y movements, paired with a precision-crafted servo-controlled Z-axis to elevate photovoltaic simulators along a three-story-tall vertical tower. This mobile-robot gantry design proved to be the most cost-effective option, significantly simplifying the overall system architecture.
.
The body’s movement system should maintain a vertical posture.
Following the deployment of the photovoltaic simulator payload, the entire mobile-robot gantry required structural reinforcement to support the weight and ensure that the simulator’s LED arrays remained precisely aligned with the photovoltaic array. To ensure the subframe’s integrity, a substantial amount of finite ingredient evaluation was necessary, verifying its ability to withstand the stresses of load hoisting while also surviving seismic events without compromising stability.
The absolute constructability of the movement system must be massive, enabling it to execute a flawless flip at the end of a deployment within a remarkably constrained floor plan?
Constructed to test the PPE’s panels, NASA can now leverage its movement system to validate future space-bound technologies.
Heavy cantilevered lifting handles forces
The 240 photovoltaic simulator heads are arranged within a pantographic morphing array comprising three balanced pivoting segments that transition seamlessly between two distinct configurations: a rectangular formation measuring 2 feet by 18 feet. grid and a 6-by-6-ft. grid. Due to the array’s activation, it applies excessive secondary forces that impact the movement system’s physical structure.
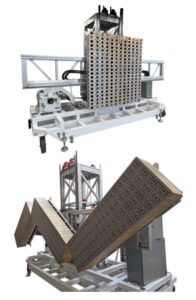
A precision-crafted prototype features a patented pantographic system, comprising three harmoniously aligned pivoting segments, which accommodate multiple LED-based light sources nestled within strategically designed open slots. Supply: Bell-Everman
To mitigate the forces at play, our design employed oversized linear bearing rails in conjunction with high-performance cross-curler bearings, measuring a robust 8 inches in length. Ethernet communication enables reliable data transfer across long distances with minimal latency and high reliability, thereby ensuring seamless transmission of critical information. The device is capable of handling a maximum load of 40 kilowatts of electrical energy per phase.
The innovative array and morphing technologies converge to define a cutting-edge aircraft weighing approximately 3,500 pounds? The cantilevered load on the vertical tower necessitates a counterbalance for each stability second, ensuring masses on the tower remain near impartial buoyancy.
The gross motion of the mixed payload and LED array is provided by a 10,000-lb-capacity system. drum hoist. Vertical movement is achieved through the use of a single crane, paired with drives and massive redundant cabling systems.
The counterbalance design effectively limits the vertical drive’s perspective to a weight disparity of 50-300 pounds, maintaining equilibrium and stability. Providing ample respiratory space for the ServoBelt Heavy LoopTrack drive, which can support up to 600 pounds of weight comfortably. of linear power.
The system’s redundancy ensures that a single drive failure won’t jeopardize the secure transmission of critical data. By threading cables through pulleys, the counterweight and payload are lifted simultaneously to their midpoint from the stored position at the rear of the device.
The unique design of this cable system enables consistent and stable buoyancy throughout its operating range.
Tower constructed piece by piece
When fully constructed, the vertical tower supporting the photovoltaic simulator load will stand at a height of approximately three stories tall. Due to its excessive height being incompatible with the surroundings where it was built, the tower was constructed in three parts.
We shortened the counterbalance cable set to enable unrestricted access underneath during comprehensive testing within our compact meeting bay’s limited ceiling height.
As the raised signal transmits vertically through the completed tower, even minor imperfections in the connections can significantly impact the simulator’s performance and diagnostic accuracy, potentially compromising overall reliability.
The tower components were seamlessly connected using an innovative, multi-generational splicing method, analogous to the sophisticated gantry systems that enable extensive travel distances. These versatile splicing joints enable effortless vertical adjustment across the splice connections.
Z-axis automation for getting round
The movement system’s actuation is manually controlled, with the exception of the Z-axis travel, which is fully automated. Given the substantial value of space-faring photovoltaic arrays such as these, it is generally more prudent to manually reposition axes of motion that pose even a slight risk of compromising the array’s integrity.
The electrically powered tug unit is responsible for transporting the entire system, whether it’s being moved away from or placed into storage. As the system approaches the PPE photovoltaic array, precise adjustments are implemented through lever arms connected to the system’s wheels. Once the correct position has been reached, the toe screws are carefully lowered to the floor.

Standing at an impressive height of three stories, the photovoltaic simulator tower is a marvel of engineering. On display, the pantographic morphing array assumes its large-scale form, measuring a substantial six feet by six feet. Supply: Bell-Everman
As a result of deploying 240 of the 500-watt LED lights in their simulated homes, a significant challenge arose from the need to manage over 120 kilowatts of energy.
The electrical system incorporates numerous breakers and branches, designed to prevent overheating and potential fire hazards by promptly interrupting power flows in the event of any short circuit or malfunction.
Calibration system is separate
To ensure optimal performance of Angstrom Designs’ programmable LED photovoltaic simulators (pLEDss), calibration against specific photovoltaic cell requirements, commonly referred to as isotypes, is crucial.
The PPE photovoltaic simulator was complemented by a calibration system, featuring an I-format gantry that cradles various solar cell types.
Known for its versatility and precision, the Calibot – a state-of-the-art I-frame gantry robot – seamlessly calibrates P LEDs heads while effortlessly transitioning between various morphing positions.
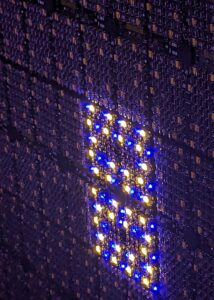
PLED modules feature advanced spectral management, ensuring precise color matching and optimal performance across a range of cell configurations, from single-junction to multi-junction designs with up to six junctions. Supply: Angstrom Designs
When calibrating the Calibot, management packaging containers are connected, and docking mechanisms maintain an optimal standoff distance, ensuring precise alignment during the process. The PPE simulator system and Calibot are expected to be co-located with NASA in the same facility.
The pantographic morphing array comprises three distinct sub-arrays, each housing 80 LED heads. Each individual subarray possesses its own distinct set of terminal blocks and associated cables.
The majority of each head’s DC power supply output is provided at a voltage level that allows for the utilization of smaller, thinner 18-gauge energy transmission wires, specifically designed to accommodate a nominal input voltage of 220 volts AC. Given the sheer volume of cabling, it is crucial to reduce bulk and space requirements for the approximately 400 cables connecting to the breaker panel boxes.
Initially inspired by the early I-format gantry design, aiming to pivot across the support structure housing two photovoltaic arrays, a floor-mounted cable track, and a data system, the estimated cost of the facility supply alone was approximately $200,000.
Thanks to the innovative mobile-robot gantry design featuring flexible extension capabilities, we were able to reduce expenses to just $6,000 and utilize only 150 feet of cable.
The company’s success could have been facilitated by a large, rail-mounted overhead crane system. With the introduction of cell gantry robots by Bell-Everman, the design was streamlined, leading to a notable reduction in system complexity and costs.

I-kind linear robots that include ServoBelt linear actuators excel in managing point-to-point movements. Supply: Bell-Everman