A novel underwater robot shows significant potential for maintaining offshore renewable energy installations. Because of its unique ability to scale vertical underwater surfaces and apply a protective coating to them, this organism is commonly referred to as the Crawfish.
Offshore energy installations, regardless of whether they capitalize on wind, tidal currents, or wave power, necessitate regular inspections, maintenance, and repair initiatives to ensure optimal performance and longevity. While utilising divers for underwater tasks can be a viable option, it’s essential to consider the significant costs and logistical challenges involved, as well as the potential risks posed to the divers’ safety?
In this local eatery, the star of the show is undoubtedly the succulent crawfish. Scientists at Germany’s Fraunhofer Institute for Marine Research developed a cutting-edge, tethered underwater device comprising two interconnected modules.
OnPrime is a commercially accessible, remotely operated automobile developed by California-based company Blue Robotics. Underneath its sleek exterior lies a sophisticated crawler unit featuring four direct-drive elastomer wheels, accompanied by an array of sensors and tools that include a digital camera, precision brush, and advanced sensor-reading head.
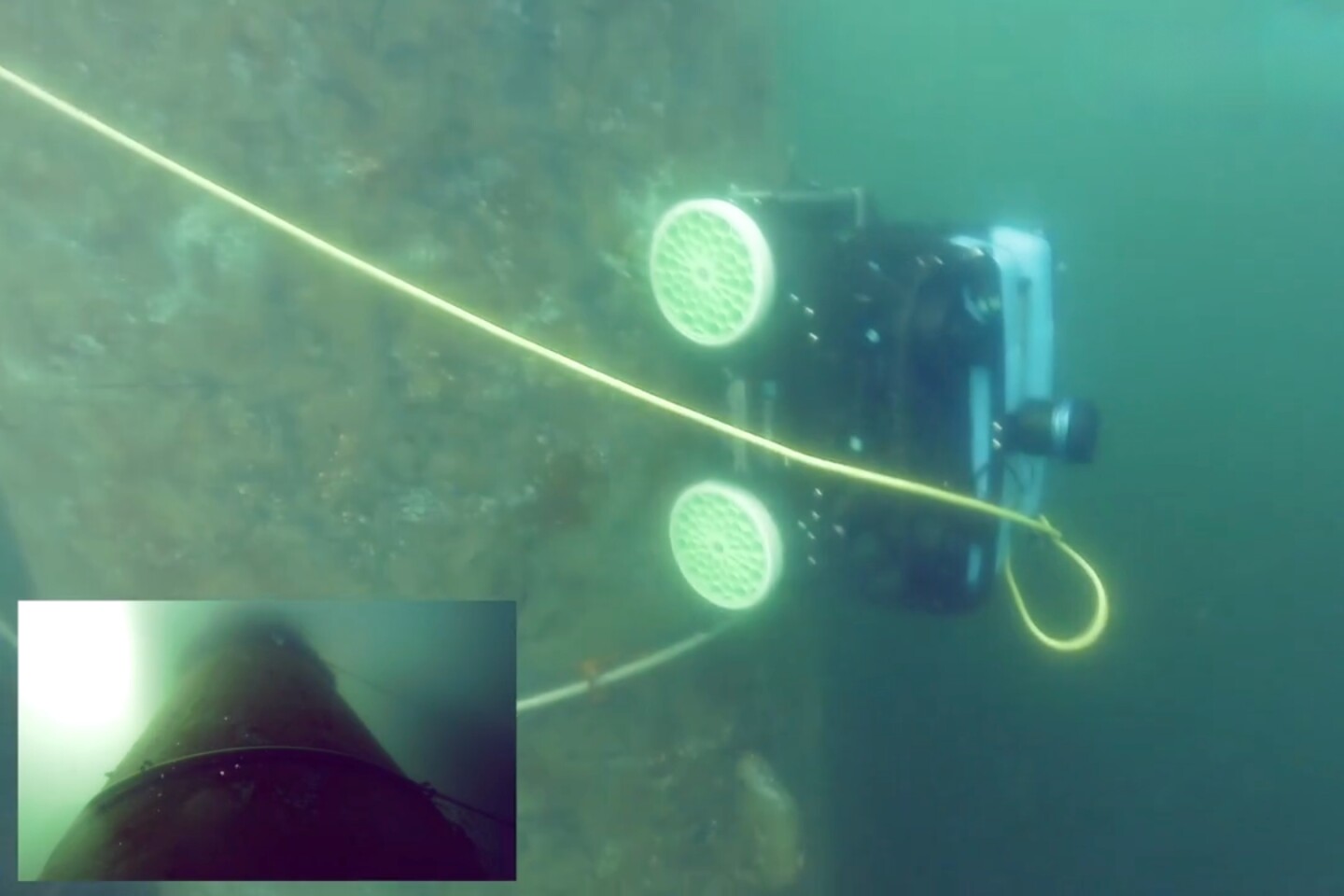
Fraunhofer
Given its lightweight design, the robotic weighs a mere 22 kilograms (48.5 pounds), allowing for easy deployment by just two or three people – cranes are unnecessary. Once submerged, a technician operating from above controls the underwater vehicle’s movement using the BlueROV2’s high-definition camera and precision thrusters.
As the BlueROV reaches the vertical floor of the platform, its thrusters exert up to 90 Newtons (20 pounds-force or 9 kilograms-force) of lateral force, effectively anchoring the Crawfish securely in position. The robot proceeds to move along the floor’s perimeter, its powered wheels propelling it forward with precision.
Because the robot employs its digital camera to conduct remote inspections for damage to the anti-corrosion coating, and its reader head wirelessly receives data from CoMoBelt sensor collars strategically placed along the platform’s length. Fraunhofer’s innovative collars utilize built-in ultrasonic transceivers to identify cracks in seam welds with remarkable accuracy.
If damage to the paint is identified, it can be repaired by injecting a two-part coating material into the robotic arm’s brush through remote operation. Defective welds can potentially be repaired using an onboard welding head.
The crawfish can dive to depths of up to 50 meters (164 feet), utilizing a maximum thrust of 50 Newtons to propel itself downward, with the capacity to sustain this activity for approximately 25 minutes on a single battery charge. Watch as these fascinating creatures display their natural behaviors of swimming freely and crawling through structures in our accompanying video.
Fraunhofer’s crawfish-inspired offshore wind farm robots?
Supply: