Typically, when an underground pure fuel pipeline sustains a leak, the damaged section must be excavated and replaced. A pipeline inspection and repair robot could render manual maintenance obsolete, potentially.
The system is currently under development by researchers at Carnegie Mellon University, spearheaded by Professor Researchers Howie Choset and Lu Li. Equipped with pipeline-laid umbilicals, the system relays real-time video and receives instructions in real-time from a remotely located surface-based crew via an umbilical cable.
At the core of the robotic’s design is its innovative mobility module, which features four robust 2-inch wheels mounted underneath and a further pair on top, providing exceptional stability and maneuverability. Six motorised wheels counterbalance against the internal pipeline walls, generating the necessary traction to haul everything else along seamlessly.
Weighing approximately 60 pounds, or 27 kilograms, this “everything else” unit comprises a power module, a mapping module that leverages high-definition optics and laser technology to create accurate 3D images of the pipeline’s interior surface, as well as a restoration module.
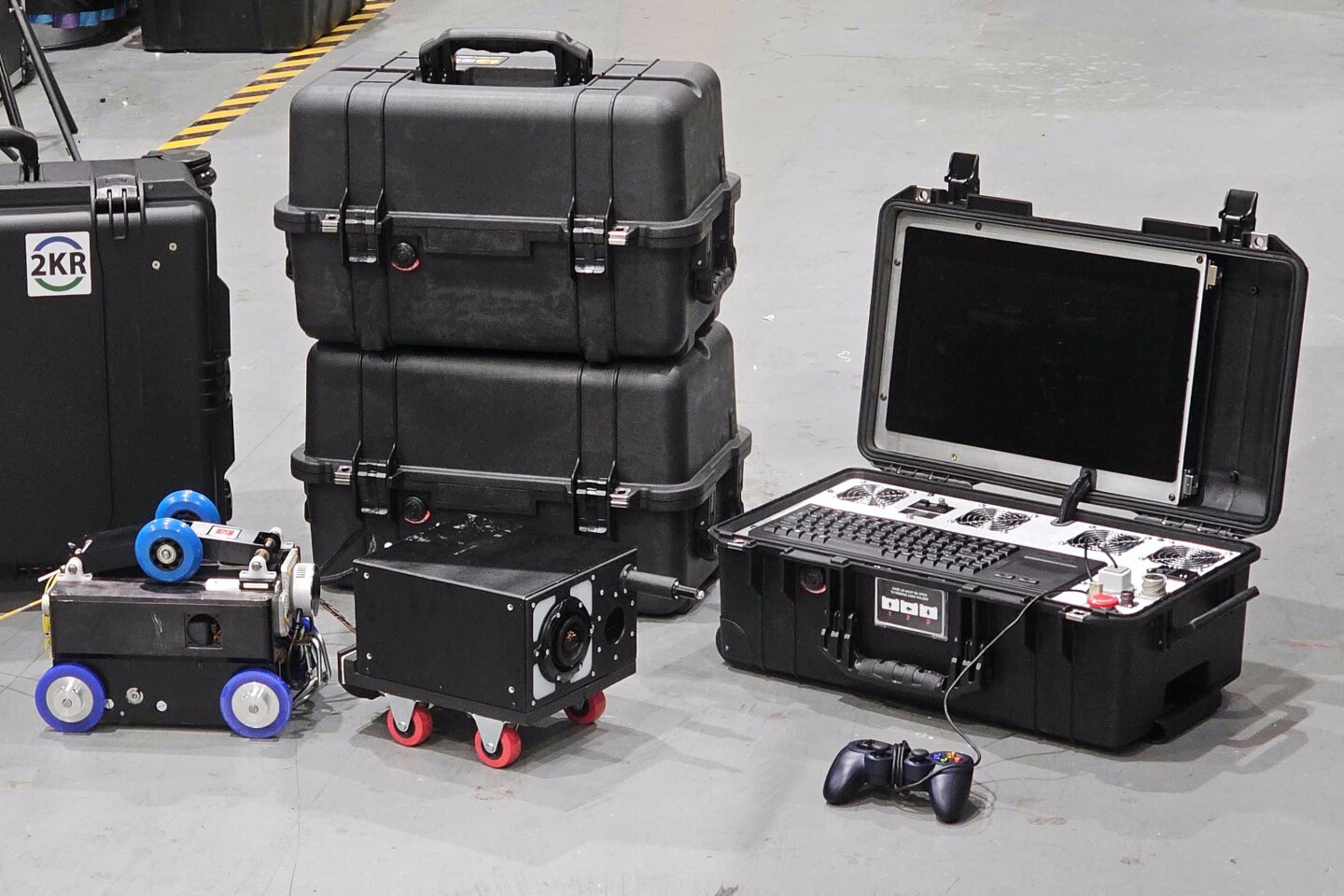
The robotic system consists of a primary unit (left) and one of its modular components, accompanied by remote-control hardware.
Carnegie Mellon College
The existing restoration module features a rotational nozzle that deposits a consistent stream of rapid-curing, impermeable adhesive onto the surface, designed to seal fissures and defects on impact. The crew identifies anomalies through the output generated by the mapping module, which is complemented by the insights provided by an AI-powered image analysis system.
Diverse restoration modules can likely be employed to accomplish tasks like sealing leaky joints between pipeline segments through welding processes.
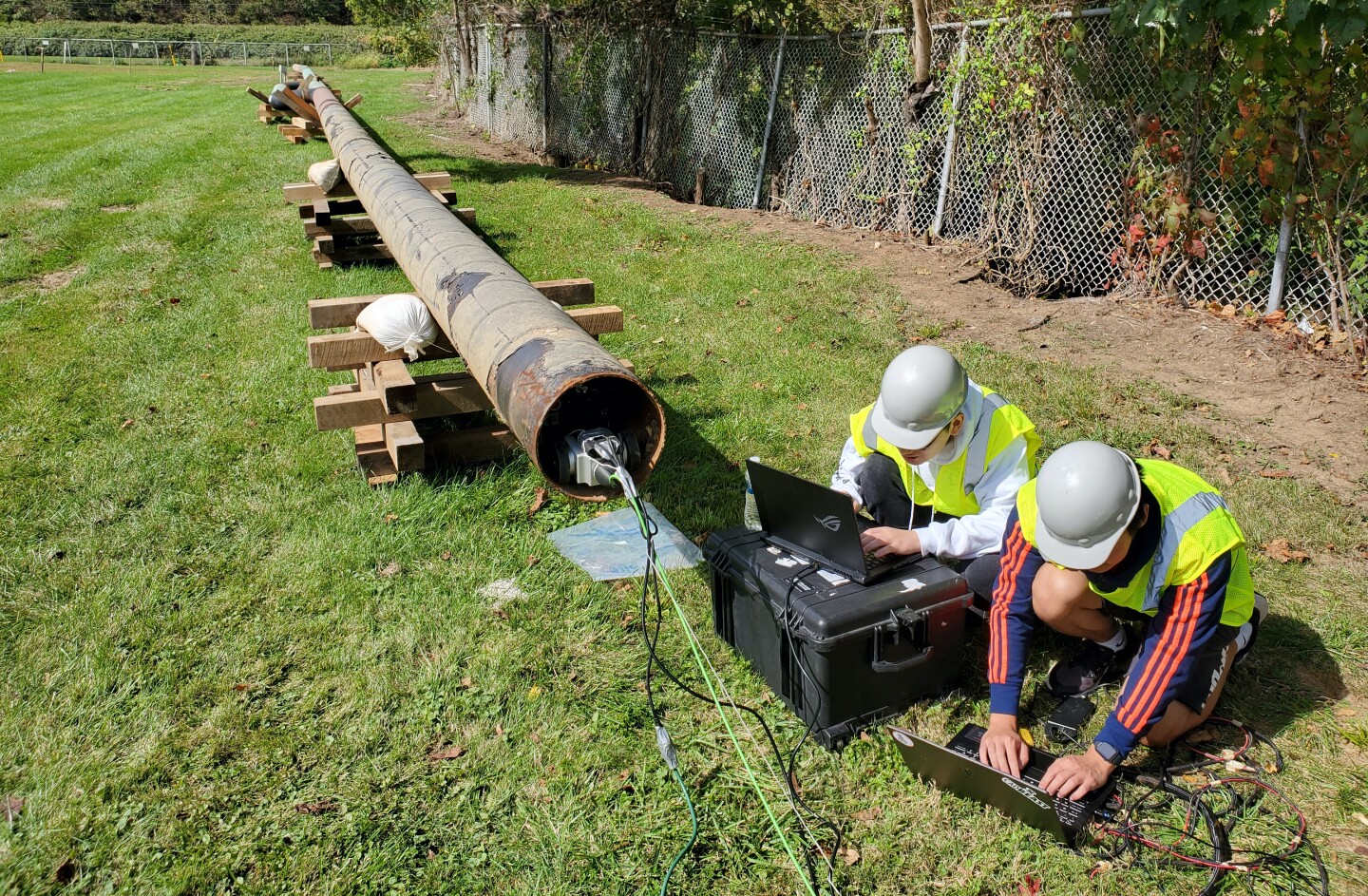
Carnegie Mellon College
The robotic system is capable of inspecting approximately 9 miles (14.5 km) of 12-inch (30.5 cm) diameter pipe within an eight-hour timeframe, whereas its resin-coating capabilities enable it to cover roughly 1.8 miles (3 km) in the same duration. With a current umbilical range of approximately 200 feet (61 meters), researchers aim to eventually expand this parameter to 2 kilometers (1.2 miles). The company is also working on a miniature version of the robot, designed to handle 6-inch (152-mm) pipes.
The US Department of Vitality, the venture’s primary funder, anticipates that employing a robot to repair pipelines internally could ultimately prove 10 to 20 times more cost-effective than traditional excavation and replacement methods.
Here is the rewritten text:
In this upcoming video, we’ll explore two perspectives on the robotic process of applying petroleum jelly as a substitute for resin to the interior of a transparent pipe component.
Petroleum Jelly Deployment with Robotic
Supply: