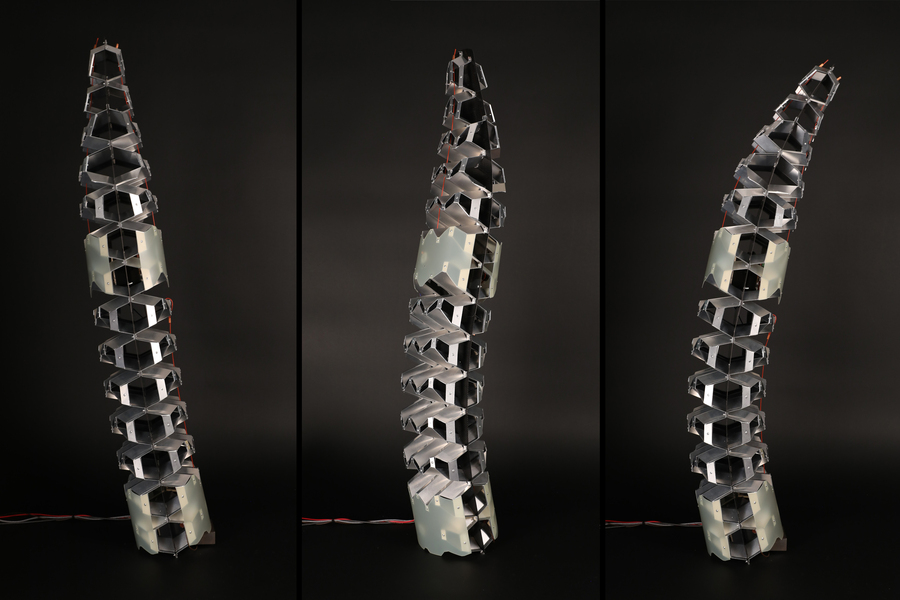
Researchers at MIT leveraged the principles of kirigami, a traditional Japanese art form of paper cutting and folding, to engineer novel materials with remarkable strength-to-weight ratios and adaptive mechanical properties that can be tailored for specific applications. These supplies can be used in various modes of transportation, including airplanes, cars, and spacecraft.
Mobile solids consist of numerous cells densely packed together, resembling the intricate structure of a honeycomb. The morphology of these cells plays a significant role in determining the mechanical properties of the fabric, alongside factors such as stiffness and strength. Bones, exemplifying the ingenuity of nature, are composed of a unique material that enables them to balance lightweight properties with remarkable stiffness and strength.
Fascinated by the intricate structures of natural materials such as bones and other mobile solids, humans have drawn inspiration from these wonders to design and engineer novel materials with tailored properties. Researchers can customize the fabric’s mechanical, thermal, and acoustic properties by modifying the geometry of the unit cells that comprise the supply. Architectural supplies are used in a variety of applications, including shock-absorbing packaging materials and heat-regulating radiator systems.
Researchers at MIT have successfully scaled up the creation of high-performance plate lattices using traditional Japanese kirigami techniques, achieving unprecedented sizes through additive fabrication methods. This technique enables architects to design and construct structures made from various materials, such as metal, offering bespoke shapes and tailored mechanical properties.
“This material is like metal cork.” According to Dr., leader of MIT’s Center for Bits and Atoms and senior writer on this subject, it’s lighter than cork yet prone to excessive power and stiffness when not managed properly.
Researchers designed a cutting-edge modular construction process that enables the fabrication of intricate structures by combining numerous small components, which can be folded and precisely assembled to form complex three-dimensional forms. By leveraging this technology, researchers have successfully created lightweight yet incredibly robust structures and machines capable of transforming and retaining their shape under defined loads.
Given the buildings’ lightweight yet robust nature, their stiffness and ease of mass production on a larger scale make them highly useful for various applications, including architecture, aircraft, automotive, and aerospace industries.
Researchers collaborate closely with Professor Neil Gershenfeld to publish papers that highlight their shared expertise, with co-lead authors comprising an analysis assistant from the Centre for Business Analytics (CBA) and an MIT electrical engineering and computer science graduate student, alongside David Preiss, a CBA graduate student, and Erik D. Demaine, a renowned professor of computer science at MIT. The analysis is expected to be presented at ASME’s.
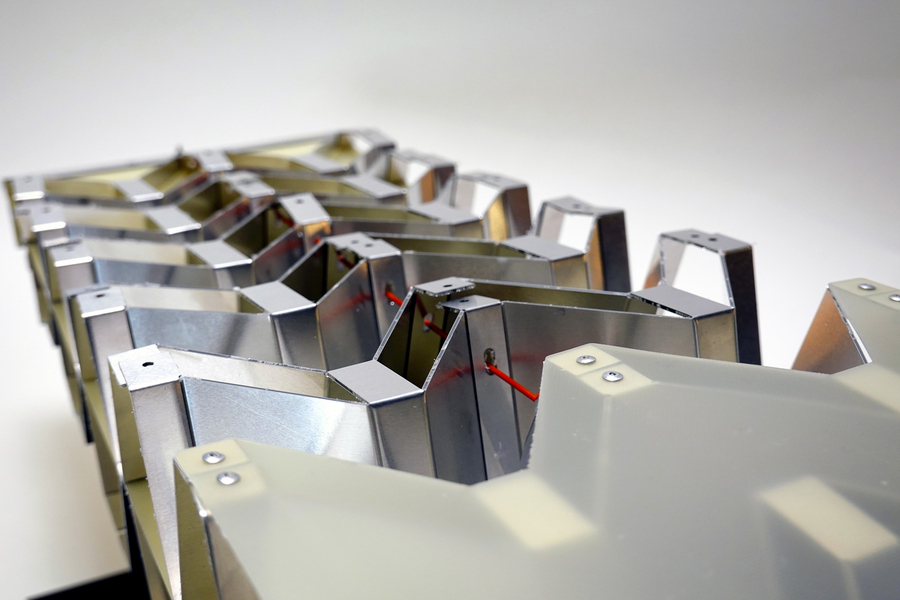
Researchers employ a novel approach to fabricate a versatile structure by initially straining metal wires across compliant surfaces, subsequently linking them to a sophisticated network of pulleys and motors, thereby allowing the construct to flexibly curve in both directions.
Fabricating by folding
Architectural supplies, such as lattices, are occasionally employed as cores in the development of composite materials commonly referred to as sandwich constructions. Consider a sandwich construction’s architecture, where interconnected, oblique beams form a lattice core nestled between a top and bottom panel. This truss lattice exhibits exceptional stiffness and power while potentially offering a remarkably lightweight design.
Plate lattices are mobile structures consisting of three-dimensional networks of plate connections, rather than traditional beam frameworks. Although high-performance buildings exhibit superior strength and stiffness compared to traditional truss lattices, their complex geometry poses significant manufacturing challenges when using conventional techniques like 3D printing, especially for large-scale engineering applications that require efficient production processes.
MIT researchers leveraged kirigami, a centuries-old art form originating in Japan’s seventh century, to overcome manufacturing hurdles.
Kirigami techniques have been employed to create plate lattices by exploiting the potential of partially folded zigzag creases. To assemble a sandwich panel, it’s essential to secure flat sheets to the top and rear surfaces of the corrugated substrate via the narrow flanges defined by the zigzag folds. This typically necessitates the use of robust adhesives or welding techniques, which can hinder production, increase costs, and pose significant scaling challenges.
MIT researchers revamped a traditional Miura-ori origami crease sample by reconfiguring its sharp features to create novel facets. The facets, akin to those on a diamond, offer flat surfaces that enable plates to be securely fastened using bolts or rivets.
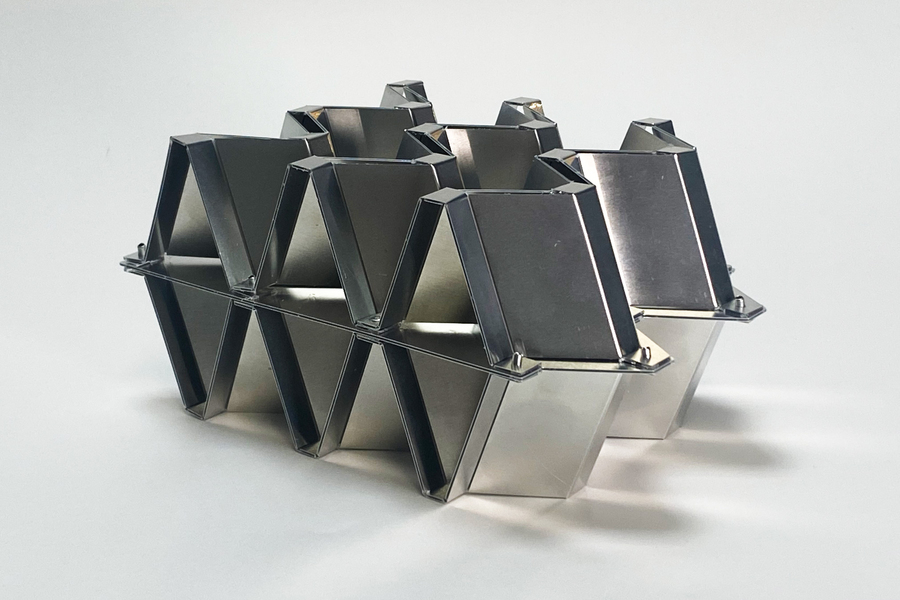
The researchers at MIT adapted a standard Miura-ori sample, typically featuring sharp creases in its origami design, to redefine these crevices as distinct features. The facets of the diamond provide flat surfaces that enable easy attachment of plates via bolts or rivets.
While plate lattices outshine their beam lattice counterparts in terms of power and stiffness, they manage to achieve this superior performance while maintaining a consistent weight and internal structure, according to Parra Rubio. Researchers have successfully achieved enhanced mechanical properties in nanoscale materials through the application of two-photon lithography, showcasing significant advancements in theoretical stiffness and power. While plate lattice buildings have presented significant challenges, the dearth of macroscopic analysis is indeed a notable oversight. We foresee that folding is a viable route to simplified application of this metal-based plate design.
Customizable properties
Moreover, researchers can deliberately design, fold, and minimise their sample size to precisely control various mechanical properties, such as stiffness, power, and flexural modulus – the fabric’s ability to resist bending. They embed this information, along with the 3D structure, within a precise creasing map that guides the creation of intricate kirigami patterns.
Some cells may be engineered to retain their shape even under compression, while others might be adapted to flex or bend accordingly, owing primarily to the design of the folds involved. The researchers can precisely manage how various areas of the structure will deform when subjected to compression.
With their adaptable design optimized for movement, these corrugations can be leveraged to build robust robots or other dynamic applications featuring moving, twisting, and bending components.
Researchers developed a modular building program to construct larger structures resembling robots. Manufacturers create large quantities of intricate crease patterns, which are then assembled into remarkably lightweight yet exceptionally robust three-dimensional structures. Smaller structures typically exhibit fewer folds, thereby streamlining the production process.
Researchers develop a bespoke Miura-ori sample, carefully crafting a crease pattern designed to produce the desired morphological and structural characteristics. Using a single Zund slicing desk, they exploit its capabilities to produce a precise, flat metallic sheet, which is then folded into its intended three-dimensional shape.
To manufacture complex products like automobiles and airplanes, a substantial investment is required for tooling. This manufacturing process is tool-free, similar to 3D printing. While our approach diverges from 3D printing, we can actually dictate the parameters for document materials’ properties, notes Gershenfeld.
Using their innovative approach, researchers fabricated lightweight aluminum structures that exhibited a remarkable compression strength exceeding 62 kilonewtons, while still maintaining an impressively low mass of just 90 kilograms per square meter. meter. Cork has a density of approximately 0.1 grams per cubic centimetre, which translates to around 100 kilograms per square metre. The metal’s structures had proved remarkably resilient, capable of withstanding an astonishing threefold increase in power compared to standard aluminum corrugations.
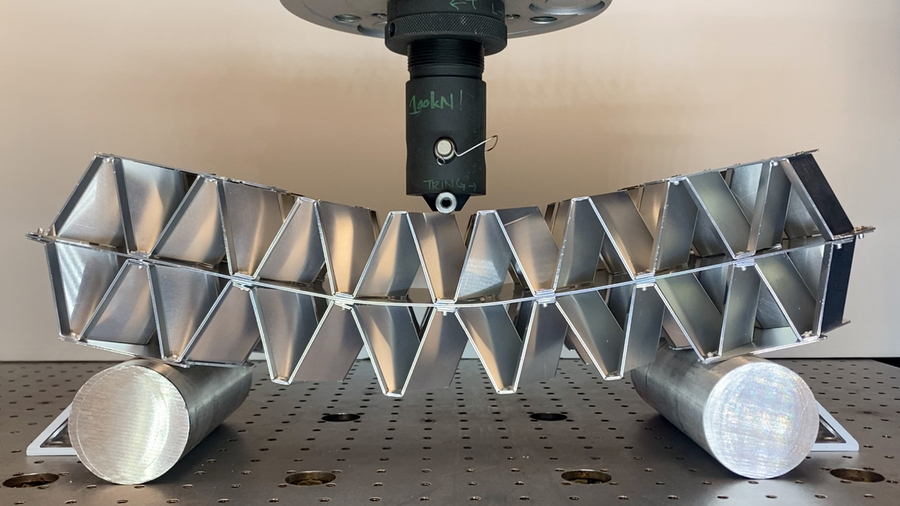
Researchers leveraged their innovative approach to engineer aluminium structures that exhibited a compressive strength exceeding 62 kilonewtons, yet weighed only approximately 90 kilograms per square unit. meter.
The versatile technique is particularly well-suited for various materials, including metals and composites, enabling its application in producing lightweight, shock-absorbing components for aircraft, automobiles, and spacecraft alike.
Notwithstanding the challenges, the researchers successfully developed a novel approach whose complexity was difficult to replicate. Aspiring to create intuitive Computer-Aided Design (CAD) tools for the innovative lattice structures of kirigami plate buildings, their future plans aim to make the design process more accessible. In addition to developing new designs, researchers must also uncover methods to efficiently reduce the computational costs associated with simulating a design that achieves desired properties.
“Kirigami corrugations holds thrilling potential for architectural building,” says James Coleman MArch ’14, SM ’14, co-founder of the design for fabrication and set up agency SumPoint, and former vice chairman for innovation and R&D at Zahner, who was not concerned with this work. While I excel in crafting intricate architectural solutions, prevailing methods for fabricating massive curved and doubly curved components prove to be resource-intensive and inefficient, rendering them unfeasible for numerous applications. While the authors’ expertise presents innovative opportunities for the aerospace and automotive sectors, it is likely that their cell-based method could have a significant impact on the built environment. The ability to produce a wide range of plate lattice geometries with distinct properties may enable the creation of more efficient and highly expressive structures that require fewer materials. Imagine saying goodbye to heavy structures, hello innovative architecture!
Students Parra Rubio, Mundilova, and others from MIT’s graduate program employed this system to design and fabricate three substantial, intricately folded sculptures using aluminum composite materials that exhibited a unique combination of form and functionality. Despite their imposing sizes, each painting can be measured in mere metres, while the buildings required only a few hours to construct.
At the end of the day, the innovative work presented in our papers is only possible through the mathematical and engineering foundations that we’re showcasing. While acknowledging that a purely functional approach may be sufficient, Parra Rubio believes that ignoring the aesthetic energy of our work is not necessary.
The research was supported in part by the Heart for Bits and Atoms Analysis Consortia, as well as individual grants from the American Association of University Women (AAUW) through their Worldwide Fellowship program and the Graduate Women International (GWI) via the Fay Weber Grant.
MIT Information