Take heed to this text |
Principal researcher Dr. Dr. Yongjin Kim Younger-Ki Kim, a researcher from the Division of Reliability at KIMM, spearheaded the development of an innovative automatic mooring system. What are the main business areas of Supply: the Korea Institute of Equipment and Supplies?
The Korea Institute of Equipment and Technology has developed a cutting-edge automatic mooring system designed to enhance the safety and efficiency of autonomous vessel docking operations. By designing a novel system that overcomes the limitations of traditional wire-based mooring methods, By 2025, KIMM anticipates that innovative breakthroughs will become commercially viable.
“This revolutionary automated mooring system is a groundbreaking innovation in the realm of autonomous vessel docking, poised to significantly enhance the efficiency of protected port infrastructure.” Yongjin Kim, Principal Researcher within the Division of Reliability at Korea Institute of Materials Science (KIMM). “We rely on this response to establish a groundbreaking standard for operational security and efficiency across the industry.”
The Korea Institute of Equipment and Technologies, a non-profit organisation funded by the government, operates under the Ministry of Science and Information and Communications Technology. Since its inception in 1976, the Korean Institute of Materials Science (KIMM) has made a significant impact on South Korea’s financial growth by pioneering research into crucial applied sciences related to equipment and materials, undertaking rigorous reliability assessments, and successfully commercialising innovative products.
.
To streamline the mooring process and enhance overall safety.
Prior to docking, personnel carefully secured ships to the berth by hand, using sturdy mooring lines. The technique demanded considerable tensile energy, contingent upon the ship’s precise measurements and weight. If the wire were to break, there would be a significant risk of accidents, necessitating a comprehensive mooring course that requires substantial personnel and resources.
The KIMM’s automated mooring system was specifically designed to overcome these hurdles. The robot employs vacuum suction pads to ensure safe handling and a sophisticated, four-degree-of-freedom hydraulic system for seamless automation.
New technological advancements have the potential to revolutionize the docking process, resulting in increased efficiency, precision, and reduced risk of accidents and labor requirements, according to experts.

The Standardized Setup for Quantitative Assessment of Suction Performance. Supply: KIMM
The Korean workforce garners international acclaim, poised for widespread commercialisation.
Dr. Under the leadership of President Seog-Hyeon Ryu, Yongjin Kim oversaw the workforce at KIMM. Dr. Dr. Younger-Ki Kim held the position of senior researcher.
Under the auspices of the “Improvement of Sensory Port-Autonomous Ship Connection Technology” initiative, generously supported by South Korea’s Ministry of Oceans and Fisheries, the endeavour was successfully executed. The innovation and impact of this knowledge have earned recognition from the Korea Federation of Mechanical Engineering Societies, designating it one of “Korea’s Top 10 Mechanical Technologies of the Year.”
By 2025, the effectiveness of this technology is expected to be thoroughly tested and validated at sea, following which the innovation’s potential for growth and commercialization will be realized.
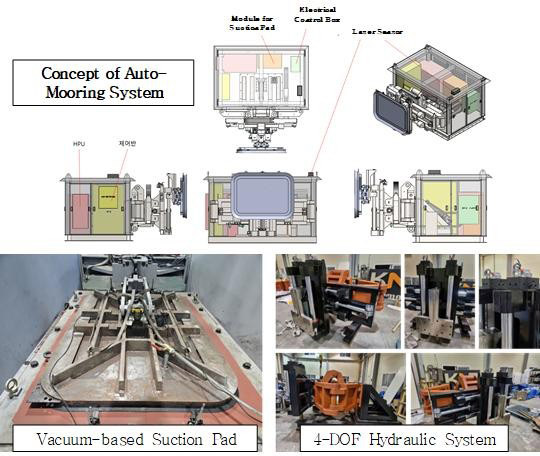
What does it take to bring a cutting-edge innovation like an automated ship-mooring platform to life? The journey begins with a brilliant idea, then accelerates through design, prototyping, and manufacturing – all while ensuring the highest levels of quality, reliability, and efficiency. Supply: KIMM