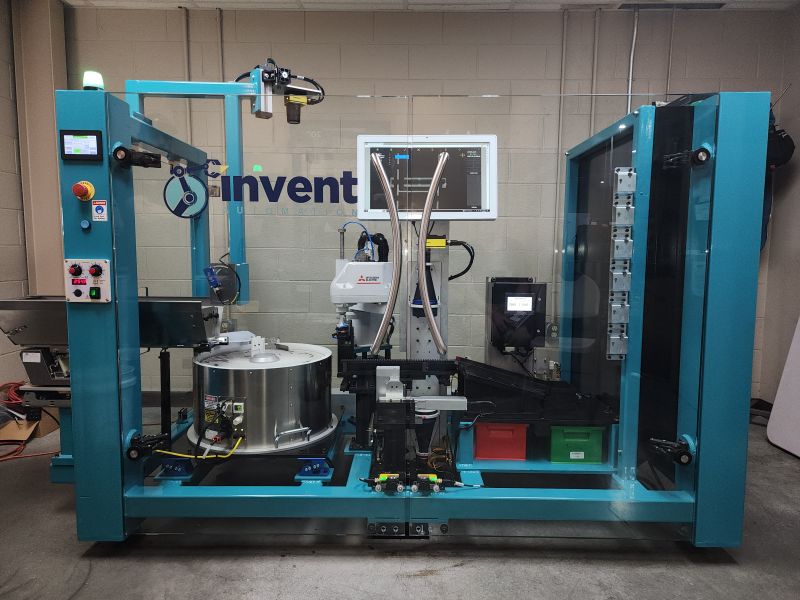
Invent Automation, leveraging DENSO’s expertise, integrates cutting-edge CapSen vision technology into its automation solutions. Supply: Invent Automation
Automotive manufacturing has long reaped the benefits of careful robotic and automation implementation, with compelling reasons to justify this approach. In a world where cutting-edge technology is constantly evolving, certain complex manufacturing procedures may prove too challenging or labor-intensive for humans to execute efficiently and safely. Consequently, industrial automation technologies can significantly enhance the value proposition of both original equipment manufacturers (OEMs) and their tier one automotive component suppliers by leveraging shared innovations. Denso, a leading global manufacturer of automotive components, recently embarked on an initiative to automate a labor-intensive and repetitive tote-handling process.
To streamline operations in their Paint Supplies Warehouse (Determine 1), the company collaborated with a technology partner that developed customized 3D vision, motion planning, and management software tailored specifically for this task.
Denso collaborated with technology integrator to create a system that streamlines processes, enabling employees to work more efficiently and effectively on the factory floor with reduced physical demands. The exercise played a key role in advancing DENSO’s comprehensive initiatives to harmonize human capabilities with automation, ultimately yielding enhanced productivity and firm performance.

Determining 1: Massive, heavy tote containers filled with automotive parts are transported to and from a paint shop workspace on a conveyor system, where a collaborative robot (cobot) selects and places totes as part of an automated process. Supply: Invent Automation
DENSO’s manufacturing prowess on full display as a production line churns out high-quality automotive parts in mere minutes.
Within DENSO’s operations, specific components are coated with a low-gloss, charcoal-hued finish that not only enhances the visual appeal of the production floor but also effectively absorbs light and minimizes glare within the vehicle.
Staff loaded six totes containing plastic automotive components onto a conveyor, which was subsequently fed to an operator who manually extracted the parts and placed them into a paint booth station (Figure 2). The components were then re-packaged into the totes. Workers continually stacked or de-stacked a tote every 30 seconds, without fail, day in and day out.
The recurring motion was identified as a potential automation substitute, potentially freeing up personnel to focus on more strategically valuable tasks. Despite structural constraints on the store floor, the limitations proved an impetus for innovative thinkers to develop a compact yet versatile automated solution.
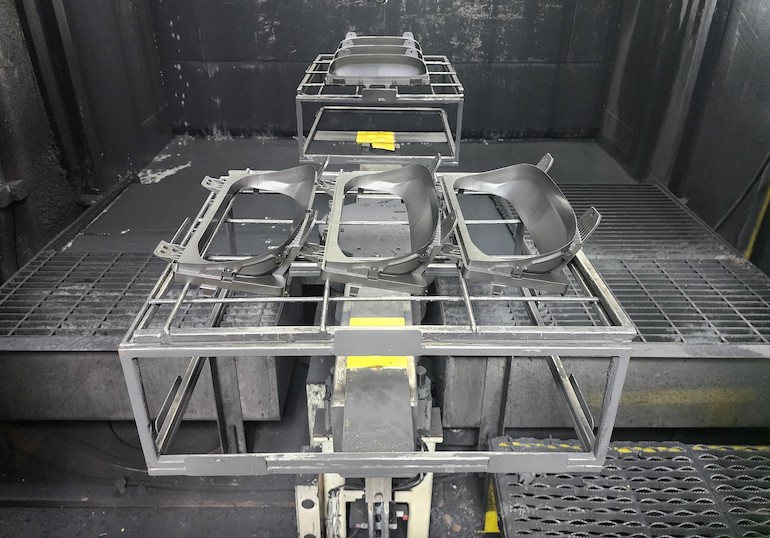
Automotive components are delivered to a paint facility where they will be coated with a low-luster finish that flattens the surface and enhances light absorption within the vehicle. Supply: Invent Automation
The newly implemented system features an inbound conveyor belt transporting totes containing unpainted objects to a state-of-the-art, six-axis collaborative robot, equipped with an Intel RealSense 3D RGB depth digital camera mounted on its end-effector. The digital camera enables the robot to visually detect the tote and measure its height to make an informed decision.
The software programme, running on an industrial PC equipped with a graphics processing unit (GPU), enables the robot to autonomously plan routes, locate, select, and manipulate totes before transferring them to another conveyor belt destined for the paint finishing station. There, the components are unloaded, primed, baked in a curing oven, and inspected before being re-packaged into totes and transferred onto the conveyor system, which feeds them to the robotics station that identifies the tote, allocates its contents, and redirects them to an outbound conveyor for further processing.
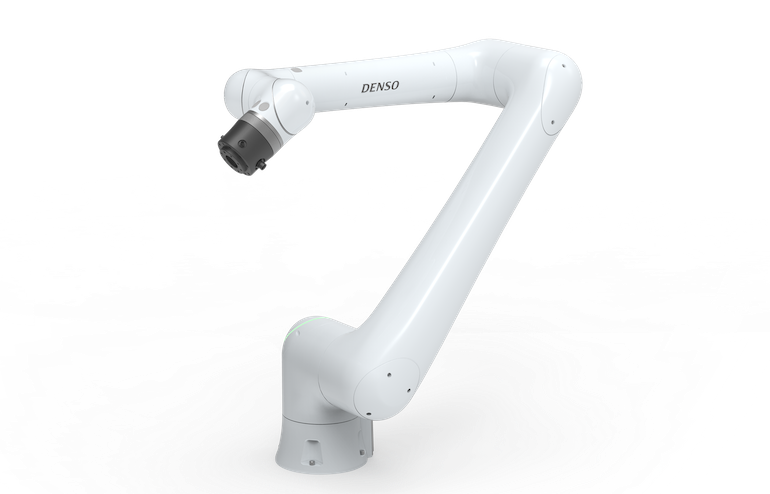
Determine three: DENSO’s CoBotta Pro 1300 collaborative robot, for reference purposes only. Supply: Invent Automation
As companions navigate maneuverability and vision challenges.
Precise actions along multiple axes are necessary for the robot to select and position large crates without causing any collisions. Within the controlled environment of CapSen PiC 2.0, the workforce could assess the robotic’s agility and ensure that every component was accessible, thereby preventing potential collisions.
Despite examining the real-world system, the workforce discovered that totes began to warp once handled by the robotic arm. To accommodate the tote’s significant weight and ensure seamless navigation without collisions within the compact cell, the team worked diligently to tailor the system accordingly.
“Our software programme leverages AI to empower robots to perform various tasks such as pick-and-place operations, including randomly selecting bins, packaging, meeting, and handling totes,” said Jared Glover, CEO of CapSen Robotics. “To tackle complex operations, where simulation environments are insufficient, we tailor our AI algorithms and models to incorporate data from the manufacturing process itself.” This enables the software programme to optimise the movement of the robot, allowing it to navigate freely without collisions, and seamlessly transition the tote throughout its cycle time.
To accomplish DENSO’s tote-handling objective, CapSen Robotics initially trained its AI software to accurately identify and pinpoint the tote’s handle. The RGB-D digital camera records images of the workspace, and sophisticated software executes machine learning algorithms that accurately detect the object, enabling the software to subsequently perform motion planning for the robot’s manipulation.
As the robotic’s finish effector comes to rest in the designated position, it is crucial to immediately recognize the load within the tote to prevent any unintended pauses or abrupt movements that might cause the tote to topple or compromise its stability. CapSen’s software program eschews traditional scales in favor of analyzing torque values on the motor, leveraging this data to accurately determine the load for informed decision-making.
According to Kevin Peek, a manufacturing engineer at DENSO, incorporating the robotic’s torque sensing capability to confirm the tote had been successfully lifted was a valuable quality control measure introduced by CapSen.
Despite encountering several machine-related challenges during the design and setup of the system, the collaborative team worked together effectively to prevent these issues from becoming major problems.
To ensure accurate stacking, the system accommodates up to six tote stacks at a time. When only two totes are involved, the issue may be manageable, but when six totes are stacked and one is misaligned, the entire structure can collapse, resulting in a significant delay throughout the process.
The system is engineered to resolve this issue by allowing robotic units to deposit totes onto a stack, followed by a slight retraction to enable the digital camera’s field of view to capture the current state of the stack. The software leveraged machine learning algorithms to identify a sweet spot between stacked totes, ensuring precise alignment, while also accurately tallying and verifying the quantity of totes in the stack.
Ultimately, the versatility of the CapSen PiC 2.0 software led to its selection for this mission, as it enables end-users to fully utilize all data generated by the various pieces of hardware. Software substitutes for programming. Like using a programmable logic controller (PLC), this approach allows for efficient development and deployment of automation solutions. There is no such instance of a Programmable Logic Controller (PLC) located within the cupboard.

“Determine 4: With its user-friendly Human-Machine Interface (HMI), CapSen PiC’s system stands out, making it effortless for operators to understand and navigate the process.” Supply: Invent Automation
Everything is handled through the intuitive CapSen human-machine interface (HMI). Operators can leverage this technology to control machinery, retrieve robotic calibration data, and visualize the feed from a digital camera, among other capabilities.
To enable non-technical staff to effortlessly operate the system as an integral part of their daily processes, our intuitive consumer interface has been carefully crafted, eliminating the need for specialized training in automation or engineering principles.
The software programme’s hardware-agnostic nature presented a distinct advantage to DENSO. Preliminary testing revealed that an autonomous cell robot successfully navigated the facility, transporting totes and various containers throughout the warehouse with precision.
CapSen’s proprietary software orchestrates the Automated Material Retrieval (AMR) system’s movements, extracting precise coordinates that guide the AMR’s navigation towards designated lanes on the movement racks, issuing calibrated corrections as needed to ensure seamless alignment.
While stacking and destacking totes is a common practice in industrial settings, this versatile solution was conceived with adaptability in mind, allowing for seamless expansion, retrofitting, or modularization within automated material handling systems.
To date, the robotic system has operated with flawless precision, effortlessly handling totes without fail, thus liberating DENSO staff from physical and emotional burdens.
Concerning the writer
Is the Government Vice President at Knoxville, Tennessee-based? Before joining the company, he had a background in manufacturing engineering and machine design, having previously worked at DENSO. With permission, this case study has been shared publicly.