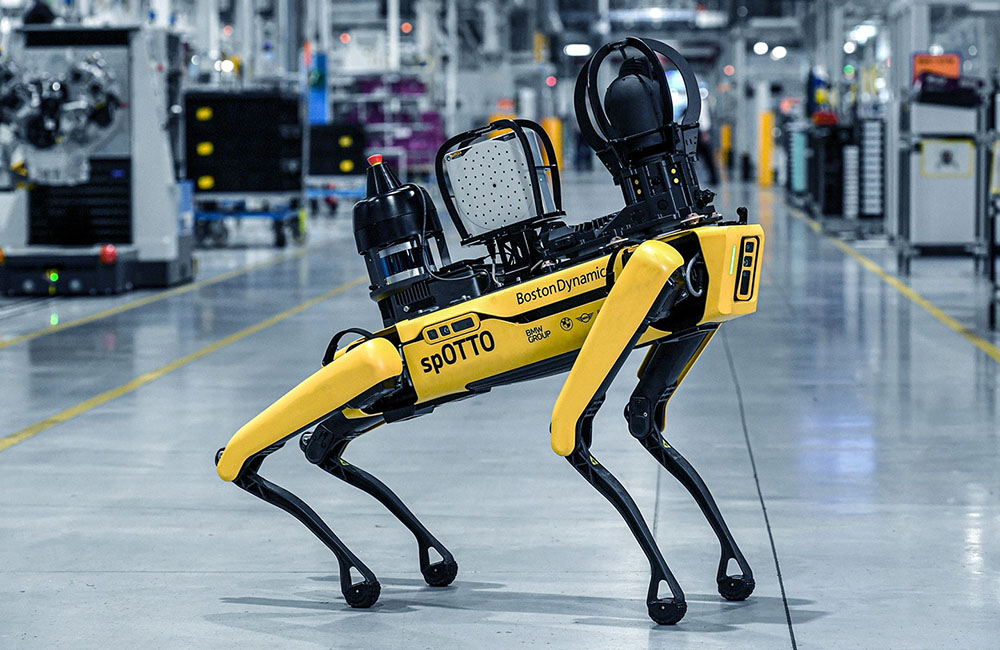
BMW acquired a Spot quadruped from Boston Dynamics to conduct automated inspections in 2023. | Supply: Boston Dynamics
BMW Group’s Hams Corridor plant close to Birmingham, England, generates oceans of knowledge within the technique of assembling its engines and elements. Making sense of that information, and, extra crucially, determining the place its blind spots are, was once like sorting via piles of puzzle items, in keeping with Boston Dynamics.
Now, with digital twin know-how and Boston Dynamics‘ Spot quadruped, the automaker stated it’s benefiting from the info it generates.
BMW produces engines, information inside Hams Corridor plant
The Hams Corridor plant machines key engine elements and assembles three- and four-cylinder inner combustion engines, in addition to V8 and V12 engines, for a spread of BMW Group autos. Its working quantity manufacturing throughout three machining strains totals 1.4 million elements per 12 months, whereas its two manufacturing amenities produce round 400,000 engines a 12 months.
At one level, inner groups have been utilizing over 400 customized dashboards to compile information related to their particular areas, all utilizing completely different strategies of knowledge entry. Hams Corridor wanted a “single supply of reality” that every one staff members might entry.
In response, the corporate developed a completely related digital twin of the ability. Creating the digital twin concerned integrating greater than 15 IT techniques right into a three-dimensional mannequin of the manufacturing facility that staff members might entry utilizing a smartphone or pill. The dual now shows dwell manufacturing information utilizing inexperienced or pink symbols to indicate the well being of a given system contained in the manufacturing facility.
BMW stated the quantity of equipment required to keep up manufacturing is immense, as is the necessity to make sure that gear is all the time working correctly by way of common inspections. Hams Corridor has an intensive tunnel system with pipes, chillers, and hydraulic panels which might be weak to air leaks. Regardless of the vital function of this gear, the digital twin revealed areas of the ability the place inspection information was lacking altogether.
It was clear the Innovation and Digitalization (I&D) staff wanted to help upkeep staff to broaden and automate inspection efforts.
Register at the moment to save lots of 40% on convention passes!
Spot covers inspections
Beforehand, the manufacturing facility introduced in contractors to examine for air leaks with specialist gear. Having the Hams Corridor upkeep staff take over these handbook inspections would take hours away from time spent on precise upkeep or repairs. The I&D staff turned to automation as an alternative.
Putting Web of Issues (IoT) sensors on gear was one possibility for gathering automated readings, however the I&D staff decided it could take years to put in all of the sensors required and show too pricey. A cell robotic outfitted with IoT sensors that would cowl the identical quantity of space, repeating the precise measurements in difficult situations could be a fraction of the fee. Boston Dynamics’ Spot robotic was the clear alternative, BMW stated.
“We acknowledged now we have a very good degree of transparency now in our manufacturing information,” stated Brad Tomlinson, the technical lead of Hams Corridor’s I&D staff. “With that transparency, we will begin to determine the gaps, and we needed to make use of Spot to fill these gaps. We didn’t have temperature information about all our belongings, or handbook dial readings and acoustic anomaly studies all the way down to specifics. That’s how we’re utilizing Spot.”
Robotic makes routine inspections
Spot at present makes use of a number of sensors for inspections, together with a thermal digicam to measure temperature, a Fluke SV600 acoustic sensor to determine air leaks, a 360° digicam, and lidar for 3D scanning. As these machines must be working 24/7, they’ve precedence on auto walks so a schedule is created for a sure station to be inspected as soon as a day, and one other station as soon as per week.
For 80% of its schedule, Spot makes routine inspections. Nevertheless, the opposite 20% of the time is spent wanting ahead.
Controlling Spot with a pill, a BMW staff member can carry the robotic to manufacturing strains for advert hoc inspections. Staff with years of expertise and who know their gear would possibly wish to use Spot to analyze a unfastened bearing or uncommon vibration. The intern will carry Spot over to take a measurement, and the staff can resolve if a restore is pressing or if it might wait.
“It’s virtually like finishing the loop from Spot to the digital twin and proper again down onto the manufacturing facility ground with the upkeep associates,” stated Tomlinson. “Spot’s really virtually absolutely embedded into the upkeep system.”
BMW shortly will get outcomes with Spot
Throughout the first weeks of inspections with the acoustic sensor, Christian Poss, the Innovation and Digitalization staff supervisor, stated Spot discovered air leaks in sudden locations, which piqued the curiosity of staff members on the manufacturing facility ground to make sure they have been monitored recurrently.
Tomlinson says an ideal instance of how the legged robotic has made operations extra environment friendly is with upkeep requests. Staff can now log into the digital twin, zoom into particular areas to view Spot’s inspection particulars, and submit a upkeep request proper there on display.
One other clear benefit of Spot is that it doesn’t require years of expertise to function, BMW stated. That is particularly necessary as a result of the corporate has an internship program for college college students. Within the U.Ok., undergraduate college students dedicate their whole third 12 months of research to knowledgeable internship.
Interns rotate via yearly, nevertheless, so BMW Group Plant Hams Corridor wanted know-how interns who might be taught and adapt shortly. Spot permits the I&D staff to scale inspections and develop different options whereas guaranteeing a high quality internship for college kids. In reality, two interns lead the Spot integration program.
“We’re working with a staff of younger professionals, which helps us be agile by way of how shortly we will roll these items out. Additionally, it provides these college students a very good internship, but it surely equally displays on how versatile the prevailing {hardware} is.” stated Tomlinson.
Register at the moment to save lots of 40% on convention passes!
Boston Dynamics to keynote Robotics Summit
Aaron Saunders, chief know-how officer at Boston Dynamics, will give a keynote discuss on the Robotics Summit & Expo. The present will likely be on the Boston Conference and Expo Middle from April 30 to Might 1. It is going to carry collectively over 5,000 builders targeted on constructing robots for a wide range of industrial purposes.
Saunders will open the second day of the present with a session on “Redesigning Atlas: Boston Dynamics on the Way forward for Humanoids.”
With over 20 years at Boston Dynamics, Saunders has held key roles, together with vice chairman of engineering. He leads multidisciplinary groups to set the corporate’s technological imaginative and prescient and align analysis and improvement with enterprise wants. Saunders holds a grasp’s in mechanical engineering from the College of Victoria and a bachelor’s from the College of Alberta.
You may also view the complete agenda right here to plan your journey and register right here. Early fowl registration for the Robotics Summit ends Feb. 28. Word that audio system are nonetheless being added.