The Belgian social enterprise AMAB employs the collaborative GoFa™ robot from ABB to feed various products into packaging machines in a collaborative manner. By implementing this system, the company boosts productivity and enhances employee safety.
Collaborative robots (Cobots) from ABB’s GoFa series support employees on packaging lines by transporting products at the correct speed and maintaining a safe distance between humans and machines.
The Belgian social enterprise AMAB acquired packaging machines to create new job opportunities. In search of a solution to feed the products seamlessly and user-friendly to the machines, the company sought. The solution should assist workers in completing their tasks at their own pace and within a defined safety distance, allowing them to work efficiently and safely.
ABB’s GoFa-Cobots deliver products to the machines. Subsequently, the workers label, package, and palletize these products. Thanks to the additional flexibility offered by cobots, AMAB can now take on more and more complex projects, creating further work for employees to manage.
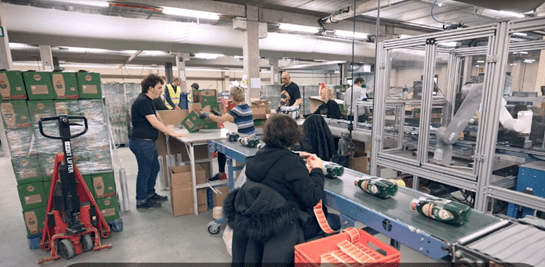
The Belgian social enterprise AMAB aims to provide job opportunities for individuals facing difficulties accessing the labor market. The company currently employs around 800 staff members and provides outsourced services for a range of activities, including packaging products. By prioritizing sustainability, AMAB recently invested in new packaging machines at its three Brussels-area locations, which reduce plastic usage by up to 80 percent.
Initially equipped with a servopneumatically controlled system that proved too fast and loud for the working environment. To resolve this downside, AMAB decided to replace the system with an ABB Cobot at one of its packaging machines. Thanks to his exceptional speed, precision, and agility, as well as the fact that he doesn’t produce any compressed air noise, the robot proved himself to be supreme for this mission. Employees do not simply work more productively – the safety of feeding products into the packaging machine has also improved significantly.
The Cobot continuously adapts to the machine’s speed, operating at up to 35 cycles per minute. By creating a buffer, workers are enabled to work at their own pace and simultaneously increase output.
“Our packaging line is a prime example of what cobots are designed for: they make the work safer, more pleasant, and ergonomic, without replacing anyone,” says Rudi Crombé, technical leader at AMAB. “With the help of ABB’s GoFa-Cobots, we can now quickly adapt to new products and take on more projects, creating additional job opportunities.”
Although the robot is equipped with comprehensive safety features enabling it to be used directly alongside humans, it is housed within a protective casing to shield private space from packaging machinery.
Following the success of this setup, the company has ordered eight more GoFa-Cobots, bringing the total to nine Cobots at all three AMAB locations. They assist AMAB in boosting productivity and delivering an attractive service to potential customers.
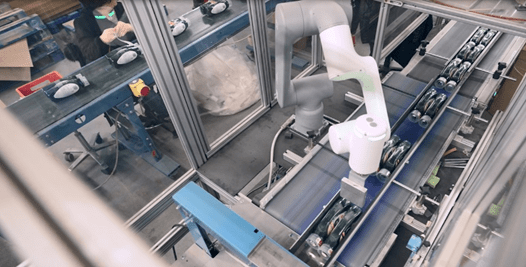
Cobots can be quickly and easily configured to meet specific production needs. ABB’s intuitive approach replaces complex coding with block-based drag-and-drop commands. This flexibility enables robots to be easily programmed for handling various products and diverse packaging tasks. Thanks to the software’s simplicity, ABB was able to train the AMAB team to handle and operate the robots within a day, without requiring any further support since then.
We opted for cobots due to their high degree of mobility. By programming their movements flexibly and eliminating noise caused by compressed air, as Rudi Crombé notes, we can achieve greater precision in our operations.
Despite initial concerns that cobots might take away their jobs, they have become the perfect workmates at AMAB for the workers. Since the introduction of cobots, employees have reported that their work has become easier and more enjoyable. The setup of cobots has also helped them to work more productively and accomplish other tasks without any job losses occurring.
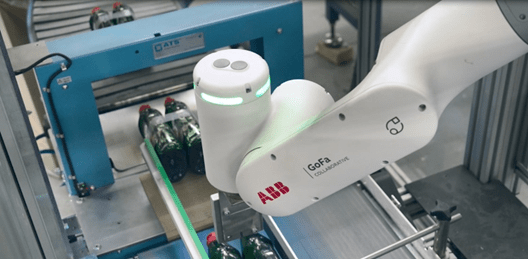